Predictive analytics is transforming the manufacturing industry, enabling companies to forecast potential issues, optimize resources, and improve production efficiency. Using data-driven algorithms, manufacturers can harness historical and real-time data to anticipate trends and make proactive adjustments, leading to cost savings, higher quality, and improved productivity.
Predictive analytics in manufacturing doesn’t just help companies see into the future, it provides actionable insights tailored to specific departments and KPIs, which can drastically improve operational outcomes.
In this article, we’ll explore how predictive analytics is applied to different manufacturing processes, the tools, and algorithms used, and how companies like CIGen can support manufacturers by integrating these advanced analytics solutions directly into their operational frameworks.
Predictive Analytics in Manufacturing: the fundamentals
At its core, predictive analytics relies on historical data combined with real-time inputs to project future outcomes. In manufacturing, predictive models use data from machinery, processes, and even external factors to provide a comprehensive forecast that can guide decision-making. These models often employ Machine Learning and Artificial Intelligence (AI) algorithms to identify patterns and correlations that may not be apparent through manual analysis.
Tools and techniques used to design and integrate Predictive Analytics into the fabric of Fabrication
- Machine Learning Models: Linear regression, Neural Networks (NN), decision tree learning, and clustering algorithms are often used to create predictive models.
- Data processing platforms /Azure-focused/: Microsoft Azure’s suite of analytics tools, such as Azure Machine Learning and Azure Synapse Analytics, provides robust data handling and model training capabilities tailored for industrial-scale data.
- IoT devices and sensors: Sensor data from IoT devices connected to manufacturing equipment can feed predictive models with up-to-the-minute information about machinery health, usage, and environmental conditions.
With predictive analytics, manufacturers can proactively address potential issues, leading to a host of specific applications. Below, we delve into seven targeted use cases where predictive analytics has driven transformative outcomes in manufacturing.
7 Impactful Predictive Analytics applications in Manufacturing
1. Predictive maintenance on assembly lines
Assembly line downtime can be costly, often impacting production schedules and customer satisfaction. Predictive maintenance uses sensor data and machine learning algorithms (like Random Forest and Neural Networks) to forecast when equipment failures might occur. By predicting wear and tear on critical machinery, companies can reduce unplanned downtime and avoid the costs associated with emergency repairs.
- Goal: Forecast machinery failures to minimize downtime.
- Technical tools: IoT sensors, time-series data analysis /with Azure Machine Learning/.
- Impact: Improved Overall Equipment Effectiveness (OEE) and extended machinery lifespan.
2. Demand forecasting for inventory management
For manufacturers using just-in-time (JIT) production models, balancing inventory is essential. Predictive demand forecasting uses past sales data and external demand indicators to optimize stock levels, helping companies avoid the pitfalls of overstocking or stockouts.
- Goal: Optimize inventory levels to meet production demands without excess.
- Technical tools: ARIMA and Prophet algorithms, /using Azure Synapse Analytics to handle large datasets/.
- Impact: Reduced inventory costs, improved cash flow, and fewer production delays.
.png)
3. Energy consumption prediction for plant operations
Energy costs can represent a significant portion of manufacturing expenses. Predictive analytics allows manufacturers to forecast energy demand, particularly during peak production times, using tools like Gradient Boosting and time-series analysis. These insights support load balancing and energy optimization strategies, reducing costs and aligning with sustainability initiatives.
- Goal: Reduce energy costs through demand forecasting and load optimization.
- Technical tools: Gradient Boosting, /Azure Databricks for energy data processing/.
- Impact: Lower energy expenses and more sustainable production.
4. Quality control enhancement through defect prediction
Maintaining quality standards is critical in manufacturing, and predictive analytics helps manufacturers proactively address potential defects. By analyzing data from past production cycles, manufacturers can identify patterns that lead to defects and take preemptive action to mitigate them. Predictive models use Support Vector Machines and clustering algorithms to help pinpoint high-risk areas in real-time.
- Goal: Anticipate defects to improve quality and reduce waste.
- Technical tools: Image recognition software, Support Vector Machines.
- Impact: Lower defect rates, higher first-pass yield, and reduced material costs.
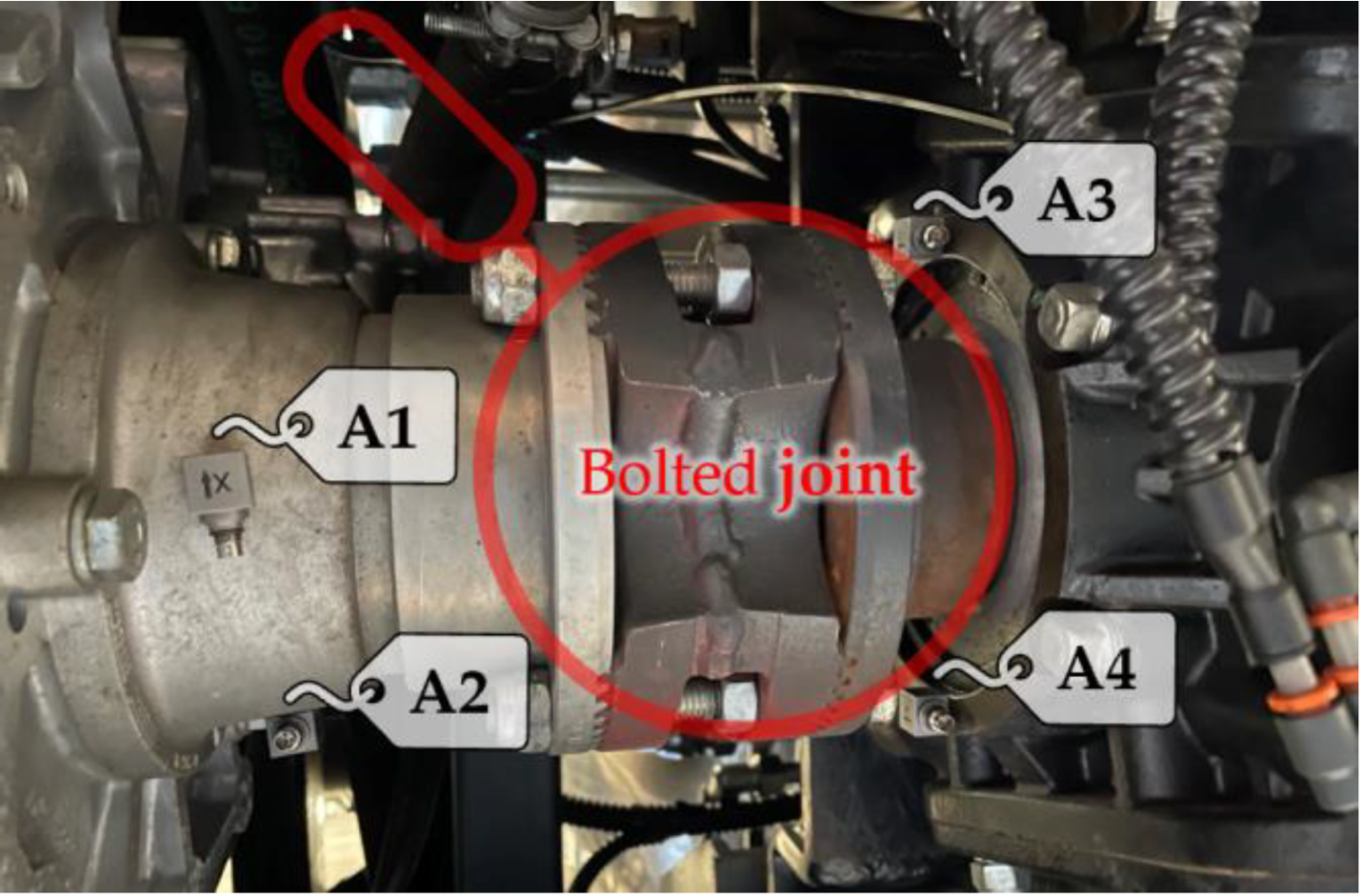
5. Supply chain risk mitigation for critical parts
Manufacturers are highly dependent on the timely delivery of components. Supply chain disruptions can lead to significant delays and production stoppages. By leveraging predictive analytics, companies can forecast supply chain risks using both internal performance data and external indicators, such as weather forecasts and political event data.
- Goal: Anticipate supply chain disruptions and mitigate risks.
- Technical tools: Bayesian networks, Monte Carlo simulations.
- Impact: Enhanced supply chain resilience and minimized production delays.
6. Production scheduling and labor optimization
In industries with fluctuating production demands, efficient labor allocation is essential. Predictive analytics models like decision trees and neural networks analyze historical staffing and production data to optimize workforce scheduling. This approach ensures that labor resources align with production needs, reducing overtime costs and avoiding production delays.
- Goal: Forecast production needs and optimize labor allocation.
- Technical tools: Decision trees, /Azure ML for workforce data analysis/.
- Impact: Lower overtime costs, improved productivity, and enhanced workforce utilization.
7. Machinery lifespan extension
For manufacturers with high-value machinery, maximizing equipment lifespan can significantly reduce capital expenses. Predictive analytics can analyze usage data to determine the ideal times for preventive maintenance. Cox regression and survival analysis, for instance, help manufacturers gauge the wear and tear on machinery and plan maintenance schedules to extend equipment life.
- Goal: Increase machinery lifespan by optimizing maintenance intervals.
- Technical tools: Cox regression, survival analysis /using Azure Synapse/.
- Impact: Reduced capital expenses and decreased maintenance frequency.
How CIGen can support manufacturing efficiency through Predictive Analytics
CIGen, specializing in Azure AI/ML software development, can help manufacturing companies implement predictive analytics solutions tailored to their specific needs. By leveraging advanced Azure tools such as Azure Machine Learning and IoT Hub, CIGen empowers manufacturers to harness real-time data insights and achieve a proactive approach to managing resources, equipment, and supply chains.
Azure-based Predictive Analytics solutions for Manufacturing
Azure’s machine learning ecosystem provides scalable, integrated tools for developing and deploying predictive analytics models across manufacturing operations. With Azure Synapse Analytics, manufacturers can unify vast datasets from different sources, creating a single source of truth that supports accurate predictions. Azure IoT Hub and Azure Time Series Insights enable real-time monitoring and data integration across IoT devices on the factory floor.
At CIGen, we can help transform manufacturing data into actionable insights by coding algorithms tailored to your operational KPIs. We will work with manufacturers to identify optimization opportunities, build predictive models around critical KPIs like OEE, defect rates, energy consumption, and inventory turnover, and ensure that our solutions integrate seamlessly with existing systems.
In conclusion
Predictive analytics in manufacturing is rapidly evolving, driven by advancements in machine learning and IoT data availability. From predictive maintenance on assembly lines to labor optimization and supply chain risk mitigation, these solutions enable manufacturers to take preemptive action, optimize resource usage, and drive cost savings.
Partnering with experts like CIGen can accelerate this journey by ensuring that predictive models are not only technically sound but also aligned with each manufacturer’s unique operational goals. By focusing on KPIs and using Azure’s industry-leading AI/ML capabilities, CIGen transforms predictive analytics from a theoretical advantage into real savings for manufacturing companies.